Grasping the situation in the accident behavior using
an experimental approach to support future fuel debris removal
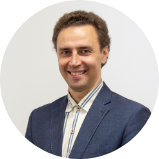
Interviewee
Dr. Anton PSHENICHNIKOV
Please tell us about the purpose and outline of your research.
My research aims to fill the gaps in knowledge about crucial data points, helping in the prediction of challenges and clarification of current decommissioning problems. When I joined the CLADS, the situation on core melting, melt progression, and material interaction during molten materials relocation inside TEPCO Fukushima-Daiichi Nuclear Power Station (FDNPS) reactors was unclear. I spent a lot of time analyzing the BWR control blade degradation, which occurs first during an accident. The onset and scale of control blade degradation strongly influence where fuel degradation starts. The mechanism of control blade degradation is now better understood, and the features that I discovered throughout my investigation, helped in the clarification of B transport during the accident. My data, I believe, will be useful in improving the severe accident codes for BWR applications developed by JAEA and other organizations.
Please tell me about the formation mechanism of fuel debris.
During an accident, the structures melt, and elements can redistribute, resulting in the formation of new materials that were not previously present in the reactor. Some of them can represent difficulties. For example, when B is mixed with steel, the resulting small particles of metal borides in a molten agglomerate make it a hard and robust material, which can become a problem. We are investigating what materials can emerge in each unit of the FDNPS after an accident, how materials redistribute in the reactors, and what properties to expect.
In our tests, above 1500 ℃, the sample was highly oxidized, with only high melting point oxides and metallic Zr remaining. Fe-containing metals relocated to lower elevations. Slightly below 1500 ℃, we observed survived control blade debris with partially reacted B4C granules. Around 1400 ℃ down to 1200 ℃, there was a monolith of a solidified melt stuck between the channel boxes. The melt was hard and robust due to dissolved B and C. This is called a metallic blockage. Under the blockage, there was only slight oxidation and melt rivulets. Some droplets detached from the blockage and fell directly to the bottom. At the bottom of the furnace, where T < 1000 ℃, we had observed the melt pile-ups and the fallen degraded parts of the test assembly.
As a result of our test program, we discovered three major types of debris: Type I–molten and then solidified metallic debris with unknown and unstable chemical composition, Type II–oxidic debris, and Type III–partially degraded parts with original geometry and chemical composition but changed microstructure (maybe metallic as assembly parts or oxidic as a fuel pellet).
As long as metallic debris is first to develop, it will relocate to lower elevations first, where it will be heated by the fuel’s decay heat, causing damage to the reactor’s lower head. Molten metallic debris is more dangerous than oxidic debris to the reactor vessel’s integrity. However, they work only in combination with each other. As soon as they breach the reactor pressure vessel and discharge to the primary containment vessel, the metallic debris spreads rapidly, cools down, and solidifies.
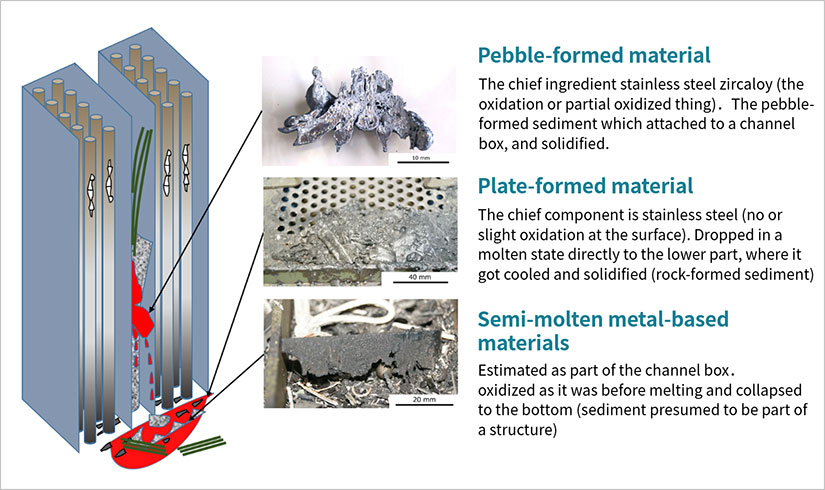
Examination product by LEISAN*
*Large-scale Equipment for Investigation of Severe Accidents in Nuclear reactors
Some pieces of Type I metallic debris can be transported to JAEA for analysis. The Type II–oxidic debris can be crushed and removed for further reprocessing in the reprocessing plant. Type III - are the partially damaged original structures. Samples of these types will be sent to JAEA for a more detailed investigation of the structure of materials. It helps in a complete clarification of the conditions of this part in the reactor core.
What kind of things can be clarified in grasping the situation inside the reactor using this device?
Using LEISAN facility, we can clarify the features of the control- blade melt formation at the beginning of the accident. This melt starts relocation and interacts with surrounding Zr-containing materials. The course of this interaction and the features of these interactions can be seen on the in situ video, that LEISAN facility can provide.
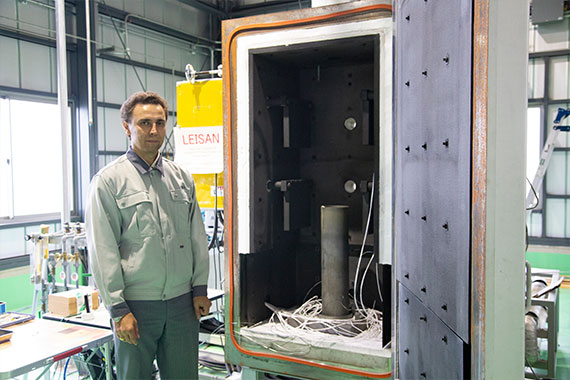
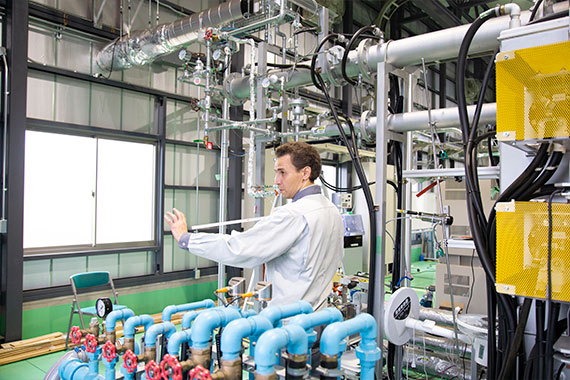
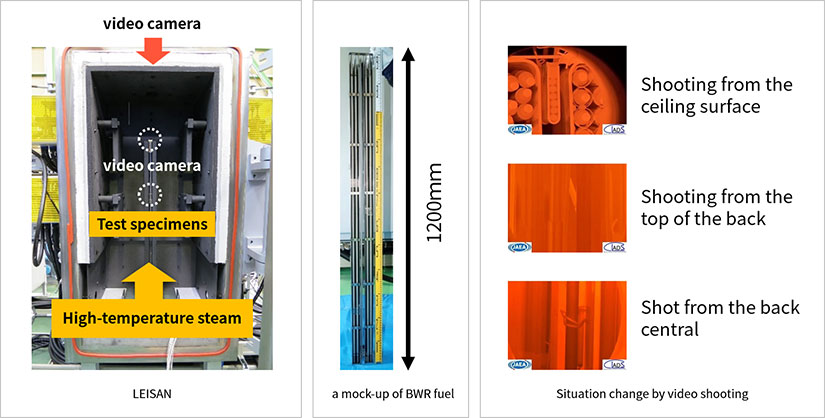
Melting and transition test by LEISAN using a mockup of BWR fuel
What issues do you think need to be addressed in order to improve the accuracy of grasping the status of fuel debris?
The main issue preventing us from grasping the status of debris is the high dose rate. Thus, current investigations in damaged reactors are limited. We are trying to reduce uncertainty by our tests, providing new data on melting features and the possibility of material interaction, predicting the debris properties and the probability gap of variation in the debris properties. At the same time, it can be a good idea to learn how to reduce the dose rate in the damaged reactors. The main contributors to the dose rate now are the isotopes of Cs and Sr. Cs emerge as a product of U fission, reacts with steam and other gaseous elements as iodine, and may deposit on various steel structures. Having high pH, Cs compounds represent a corrosive environment and corrode steel, and may attach concrete and sediments. If we learned the Cs distribution, we would remove the most intensive hot spots first and drastically decrease the radiation load on equipment and decommissioning workers. The Cs distribution must be understood. In the future, we plan to perform systematic research on the interaction of reactor structural materials with Cs and perform a large-scale test using the LEISAN facility, including Cs compounds.
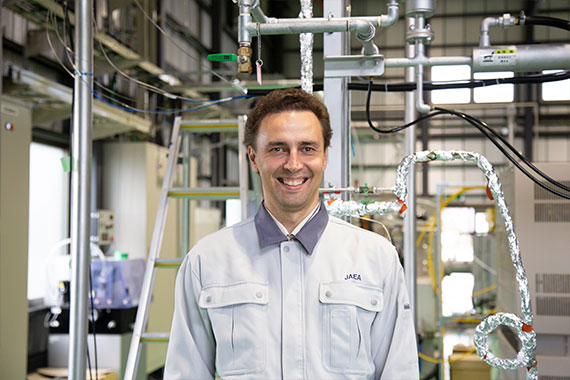
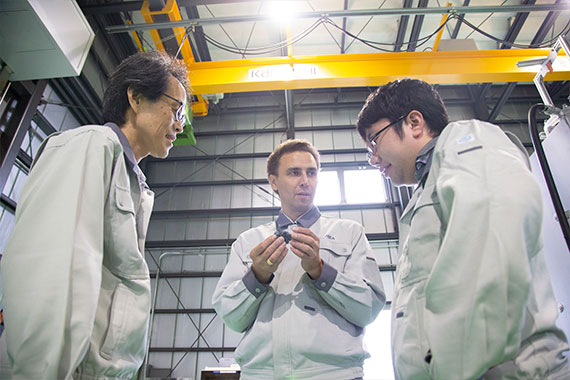
Also, what kind of work and research will the elucidated events be applied to in the future?
No one can predict the future with certainty. I expect that our work will reduce uncertainties in the metallic debris formation in all reactors and their properties (necessary for decommissioning), that we will better understand the features of molten materials and their interactions with surrounding structural materials (necessary for modeling), and that we will clarify the B behavior during the accident (necessary for scientific community). In the future, we also plan to clarify Cs behavior, which is crucial simultaneously for decommissioning, modeling, and science.